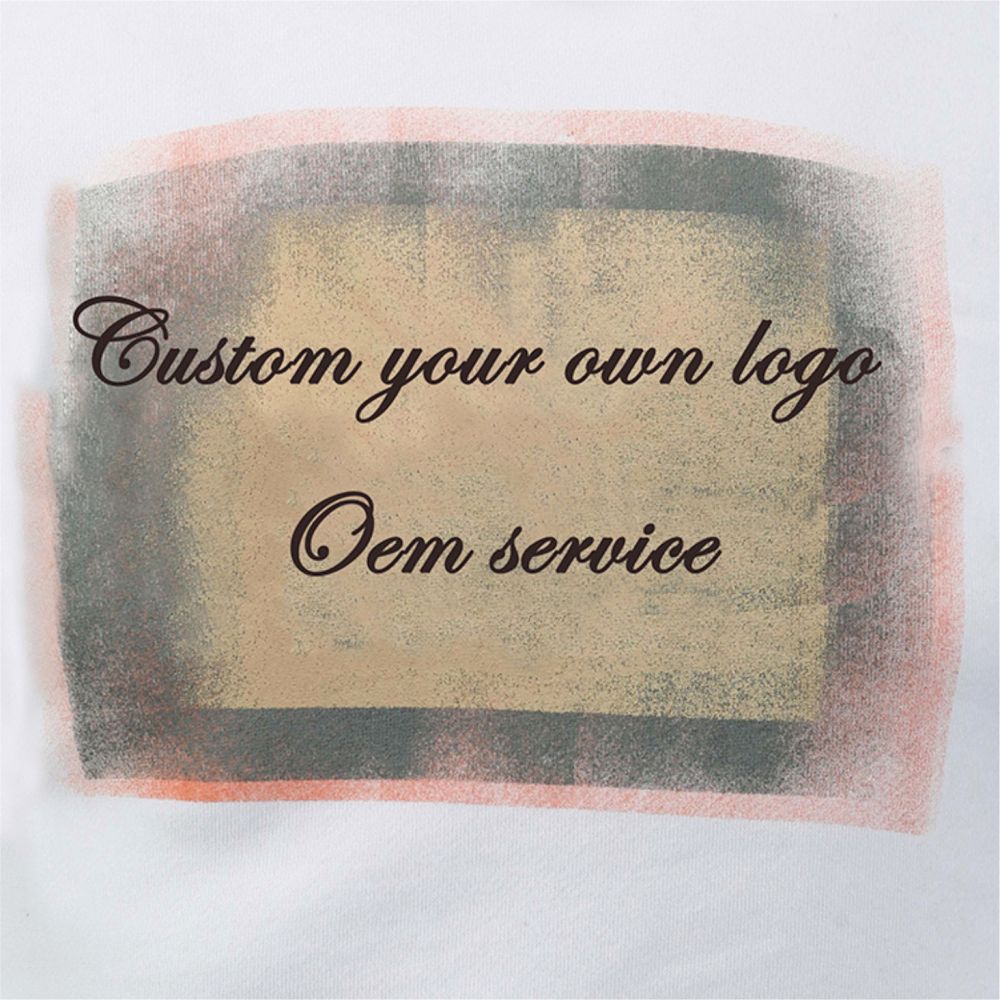
Water Print
It is a type of water-based paste that is used to print on garments. It has a relatively weak hand feel and low coverage, making it suitable for printing on light-colored fabrics. It is considered a lower-grade printing technique in terms of price. Due to its minimal impact on the original texture of the fabric, it is suitable for large-scale printing patterns. Water print has a lesser effect on the fabric's hand feel, allowing for a relatively soft finish.
Suitable for: Jackets, hoodies, T-shirts, and other outerwear made of cotton, polyester, and linen fabrics.
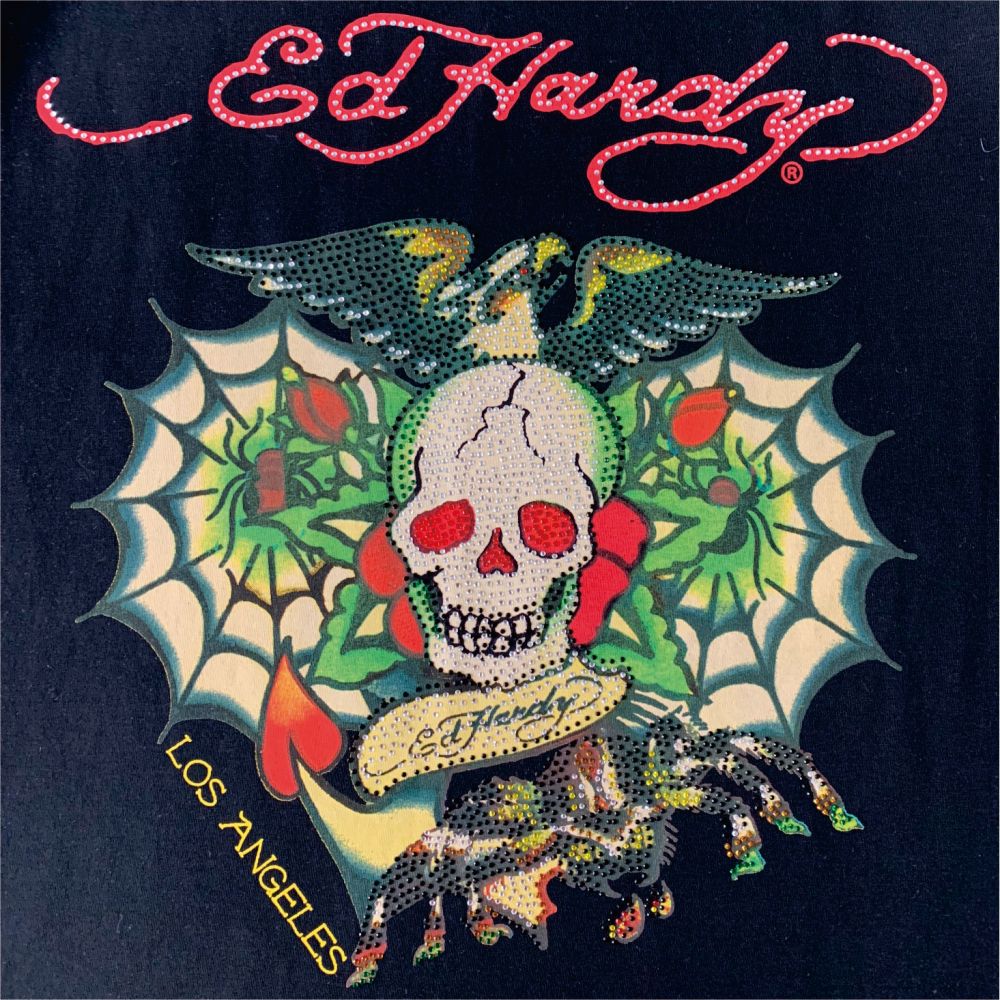
Discharge Print
It is a printing technique where the fabric is first dyed in a dark color and then printed with a discharge paste containing a reducing agent or an oxidizing agent. The discharge paste removes the color in specific areas, creating a bleached effect. If color is added to the bleached areas during the process, it is referred to as color discharge or tint discharge. Various patterns and brand logos can be created using the discharge printing technique, resulting in all-over printed designs. The discharged areas have a smooth appearance and excellent color contrast, giving soft touch and a higher-quality texture.
Suitable for: T-shirts, hoodies, and other garments used for promotional or cultural purposes.
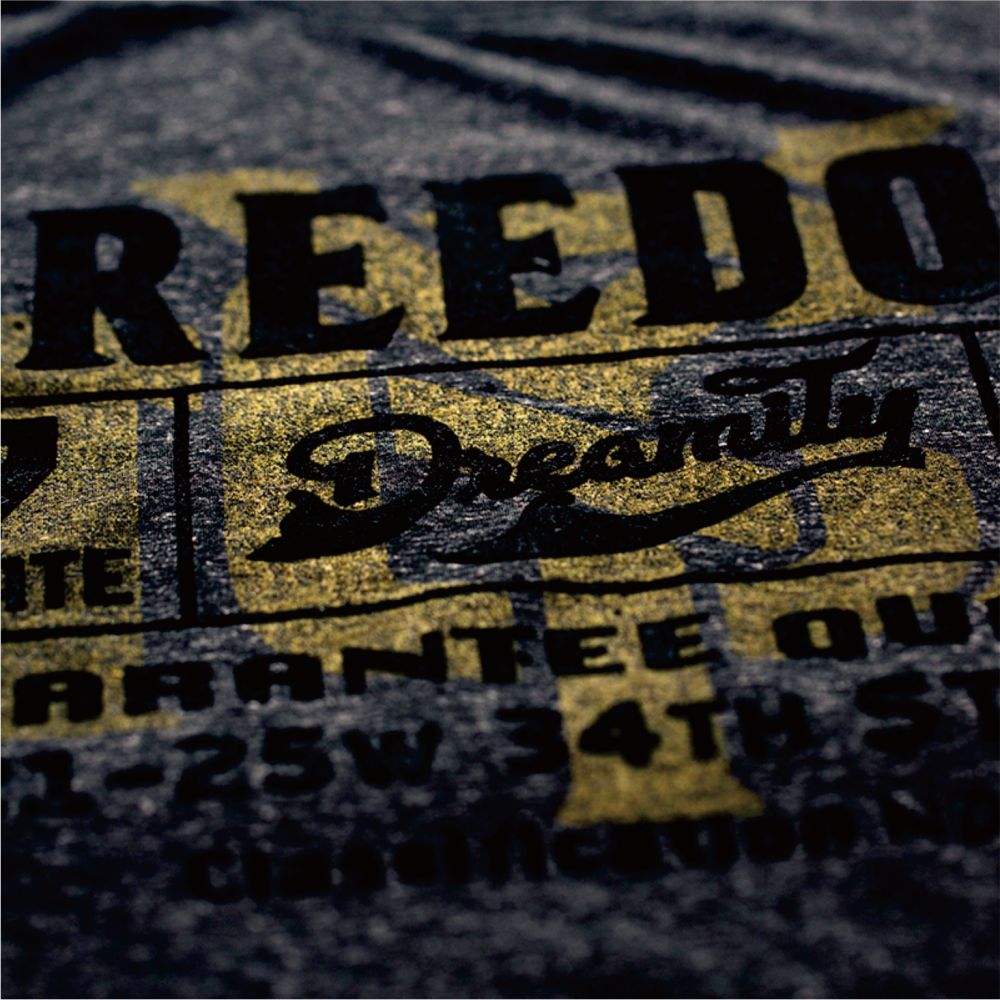
Flock Print
It is a printing technique where a design is printed using a flocking paste and then flock fibers are applied onto the printed pattern using a high-pressure electrostatic field. This method combines screen printing with heat transfer, resulting in a plush and soft texture on the printed design. Flock print offers rich colors, three-dimensional and vivid effects, and enhances the decorative appeal of the garments. It increases the visual impact of clothing styles.
Suitable for: Warm fabrics (such as fleece) or for adding logos and designs with a flocked texture.

Digital Print
In digital print, Nano-sized pigment inks are used. These inks are ejected onto the fabric through ultra-precise print heads controlled by a computer. This process allows for the reproduction of intricate patterns. Compared to dye-based inks, pigment inks offer better color fastness and wash resistance. They can be used on various types of fibers and fabrics. The advantages of digital print include the ability to print high-precision and large-format designs without a noticeable coating. The prints are lightweight, soft, and have good color retention. The printing process itself is convenient and fast.
Suitable for: Woven and knitted fabrics such as cotton, linen, silk, etc. (Used in garments like hoodies, T-shirts, etc.
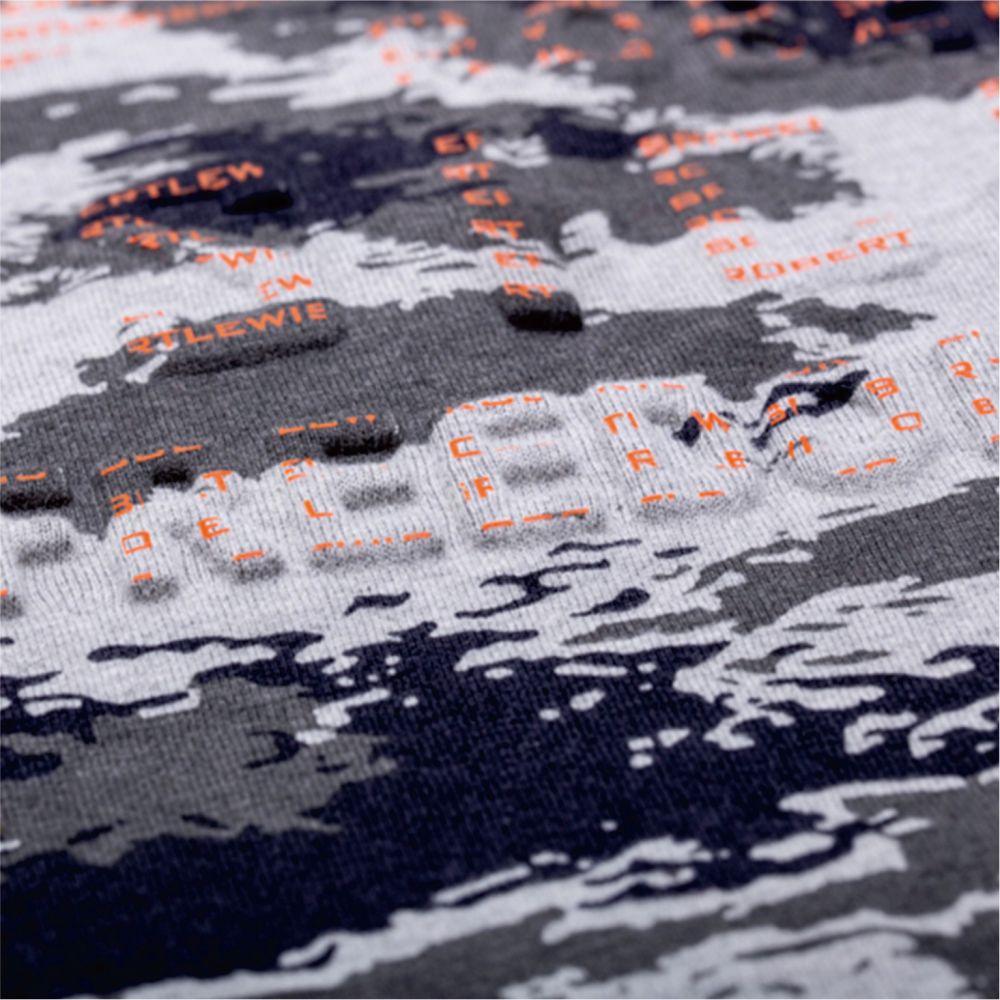
Embossing
It is a process that involves applying mechanical pressure and high temperatures to create a three-dimensional pattern on the fabric. It is achieved by using molds to apply high-temperature heat pressing or high-frequency voltage to specific areas of the garment pieces, resulting in a raised, textured effect with a distinctive glossy appearance.
Suitable for: T-shirts, jeans, promotional shirts, sweaters, and other garments.
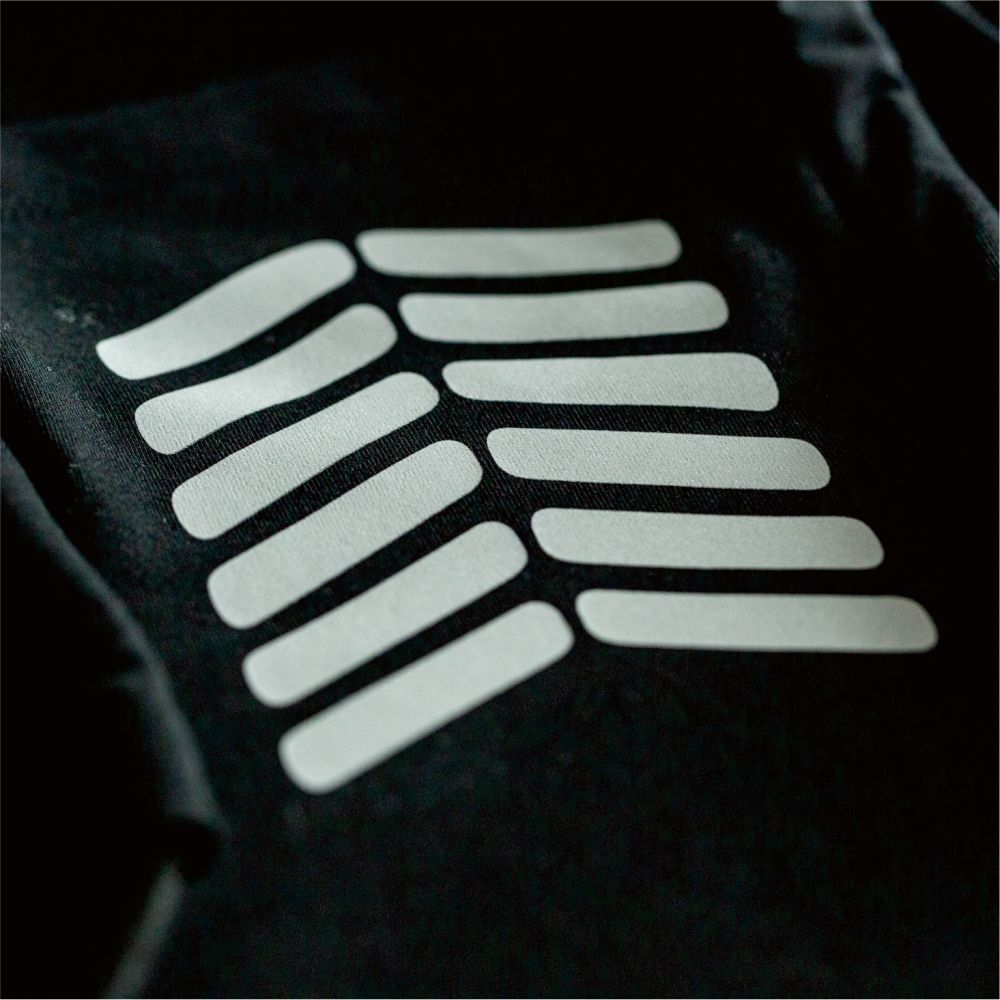
Fluorescent Print
By using fluorescent materials and adding a special adhesive, it is formulated into fluorescent printing ink to print pattern designs. It displays colorful patterns in dark environments, providing excellent visual effects, a pleasant tactile feel, and durability.
Suitable for: Casual wear, children's clothing, etc.
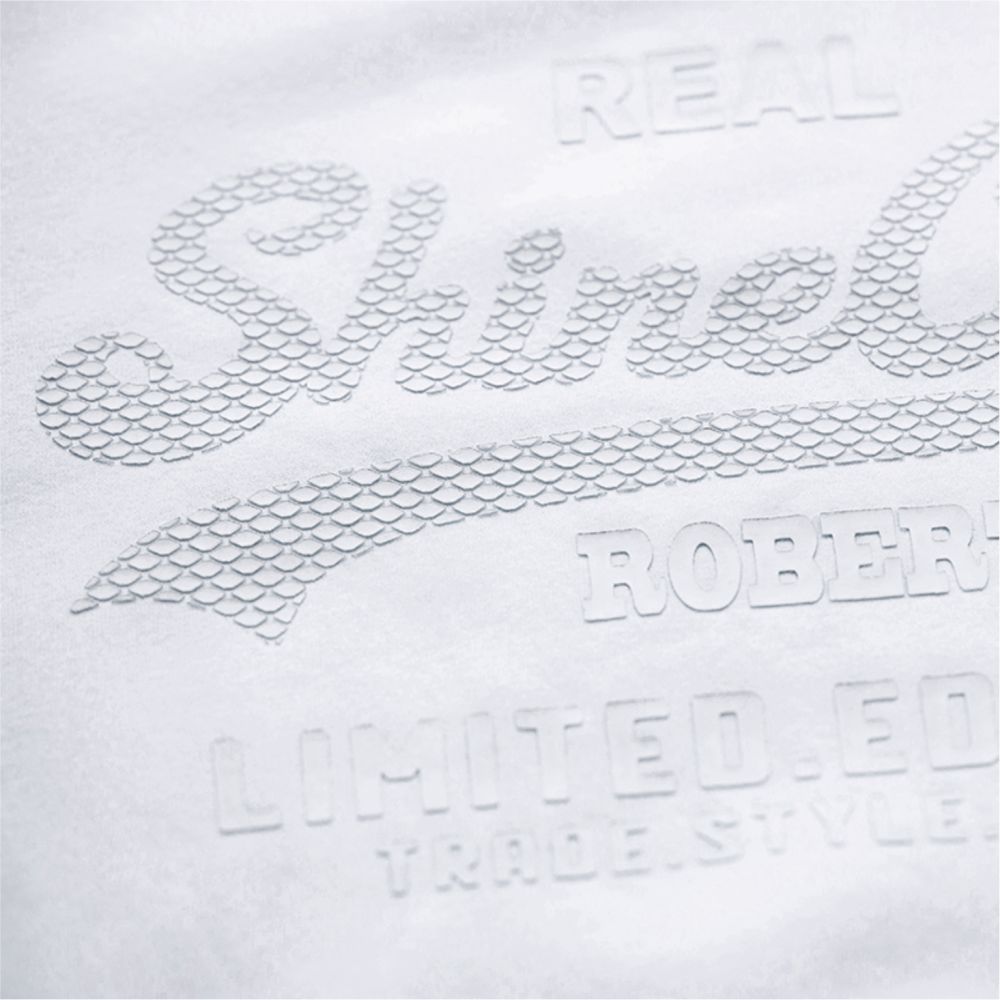
High density print
The thick plate printing technique uses water-based thick plate ink and high mesh tension screen printing mesh to achieve a distinct high-low contrast effect. It is printed with multiple layers of paste to increase the printing thickness and create sharp edges, making it more three-dimensional compared to traditional rounded corner thick plates. It is mainly used for producing logos and casual style prints. The material used is silicone ink, which is environmentally friendly, non-toxic, tear-resistant, anti-slip, waterproof, washable, and resistant to aging. It maintains the vibrancy of the pattern colors, has a smooth surface, and provides a good tactile sensation. The combination of the pattern and the fabric results in high durability.
Suitable for: Knitted fabrics, clothing mainly focused on sports and leisure wear. It can also be used creatively to print floral patterns and is commonly seen on autumn/winter leather fabrics or thicker fabrics.
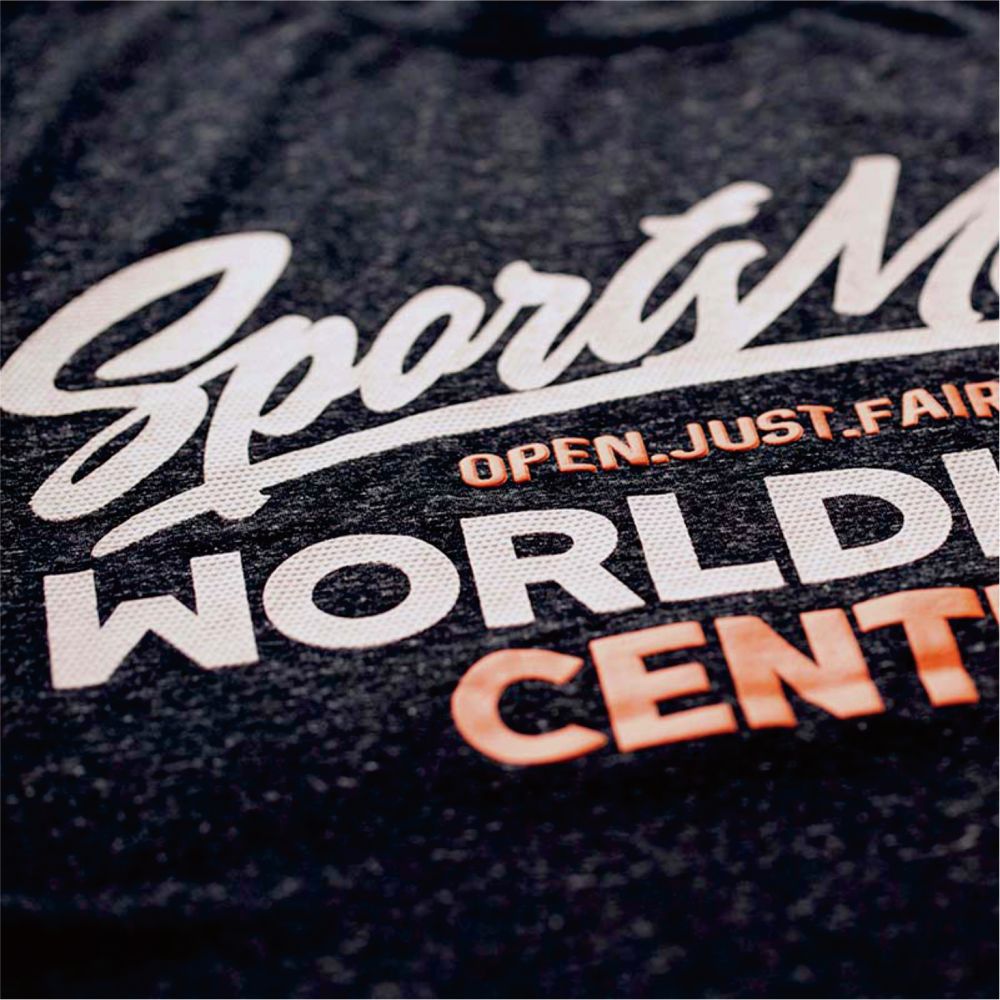
Puff Print
The thick plate printing technique uses water-based thick plate ink and high mesh tension screen printing mesh to achieve a distinct high-low contrast effect. It is printed with multiple layers of paste to increase the printing thickness and create sharp edges, making it more three-dimensional compared to traditional rounded corner thick plates. It is mainly used for producing logos and casual style prints. The material used is silicone ink, which is environmentally friendly, non-toxic, tear-resistant, anti-slip, waterproof, washable, and resistant to aging. It maintains the vibrancy of the pattern colors, has a smooth surface, and provides a good tactile sensation. The combination of the pattern and the fabric results in high durability.
Suitable for: Knitted fabrics, clothing mainly focused on sports and leisure wear. It can also be used creatively to print floral patterns and is commonly seen on autumn/winter leather fabrics or thicker fabrics.
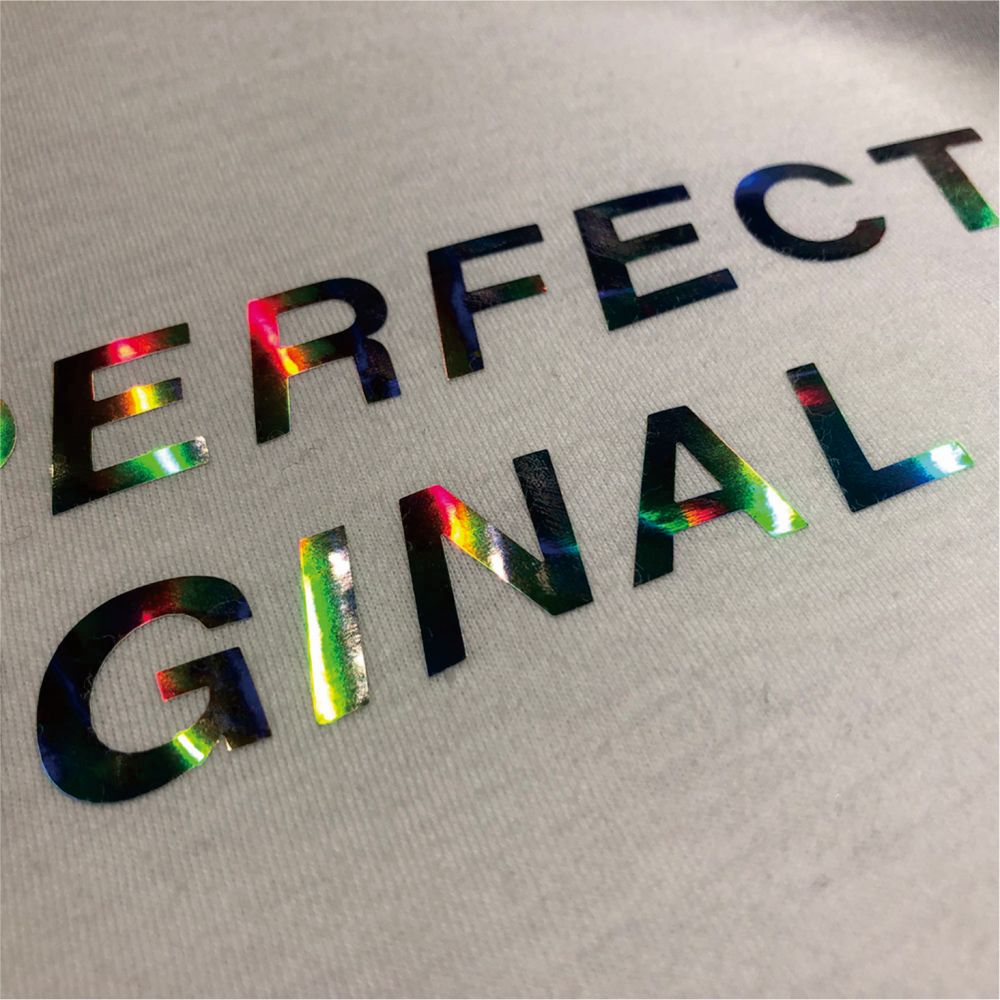
Laser Film
It is a rigid sheet material commonly used for garment decoration. Through special formula adjustments and multiple processes such as vacuum plating, the surface of the product exhibits vibrant and varied colors.
Suitable for: T-shirts, sweatshirts, and other knitted fabrics.
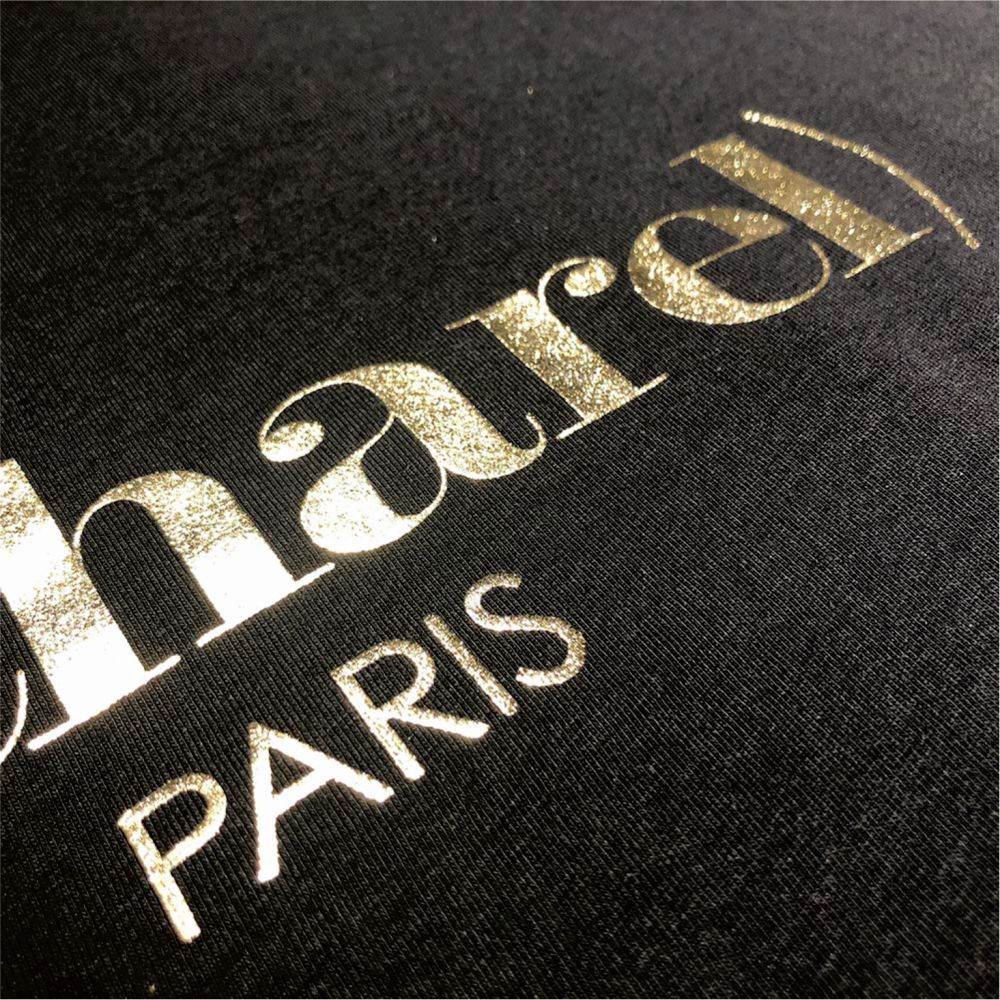
Foil Print
It is also known as foil stamping or foil transfer, is a popular decorative technique used to create a metallic texture and shimmering effect on clothing. It involves applying gold or silver foils onto the fabric surface using heat and pressure, resulting in a luxurious and stylish appearance.
During the garment foil printing process, a design pattern is first fixed onto the fabric using a heat-sensitive adhesive or printing adhesive. Then, gold or silver foils are placed over the designated pattern. Next, heat and pressure are applied using a heat press or foil transfer machine, causing the foils to bond with the adhesive. Once the heat press or foil transfer is complete, the foil paper is peeled off, and leaving only the metallic film adhered to the fabric, creating a metallic texture and sheen.
Suitable for: Jackets, sweatshirts, T-shirts.
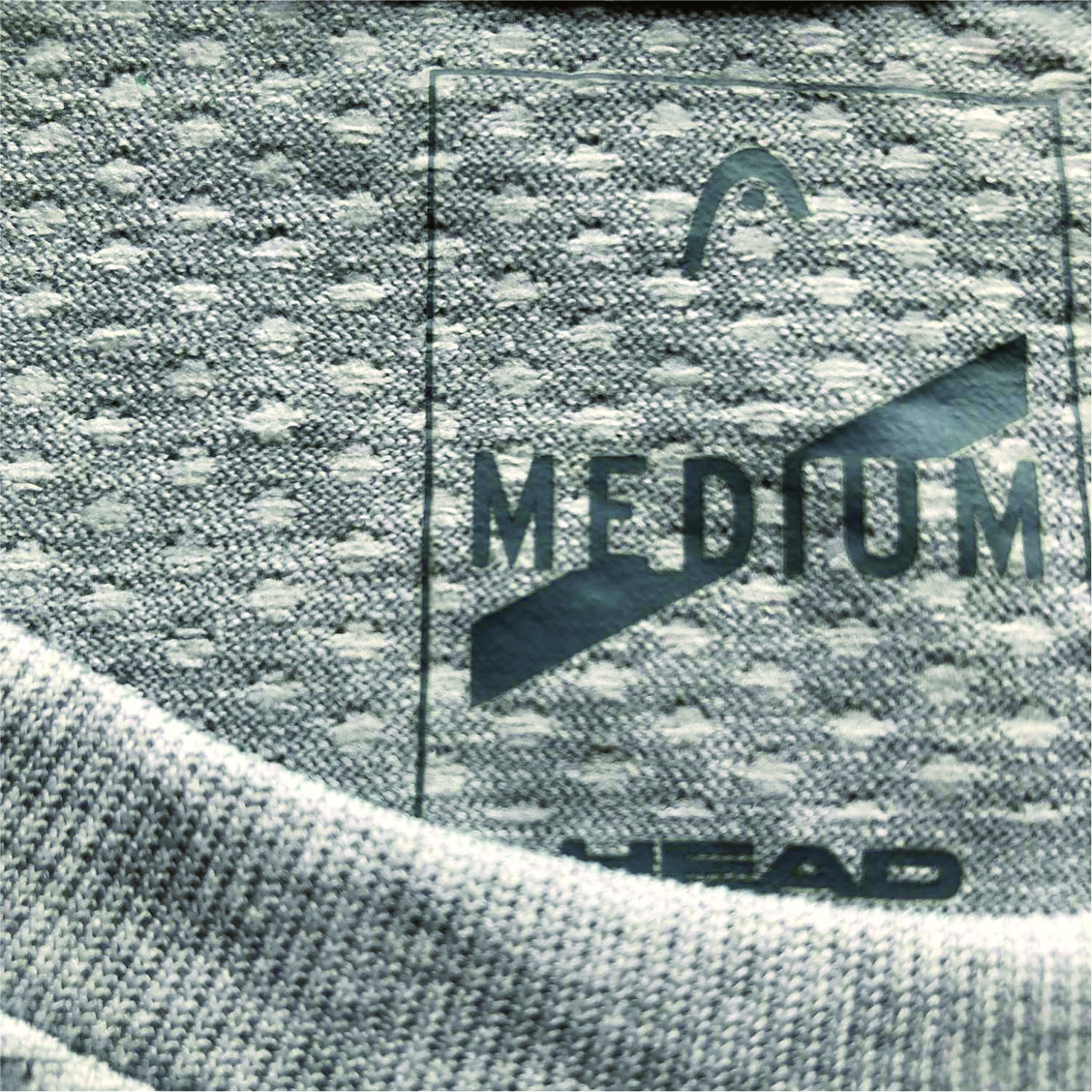
Heat Transfer Print
It is a widely used printing method that transfers designs from specially crafted transfer paper onto fabric or other materials using heat and pressure. This technique enables high-quality pattern transfers and is suitable for a variety of materials.
In the heat transfer printing process, the design is initially printed onto specialized transfer paper using an inkjet printer and heat transfer inks. The transfer paper is then firmly applied to the fabric or material intended for printing and subjected to the appropriate temperature and pressure. During the heating phase, the pigments in the ink vaporize, penetrate the transfer paper, and infuse into the surface of the fabric or material. Once cooled, the pigments become permanently fixed to the fabric or material, creating the desired pattern.
Heat transfer printing offers numerous advantages, including vibrant and long-lasting designs, compatibility with a wide array of materials and shapes, and high production efficiency. It can produce intricate patterns and details and can be completed relatively quickly for large-scale printing projects.
Heat transfer printing is extensively utilized in the apparel industry, home textiles, sports equipment, promotional products, and more. It allows for customized designs and decorations, catering to the diverse needs of the market.
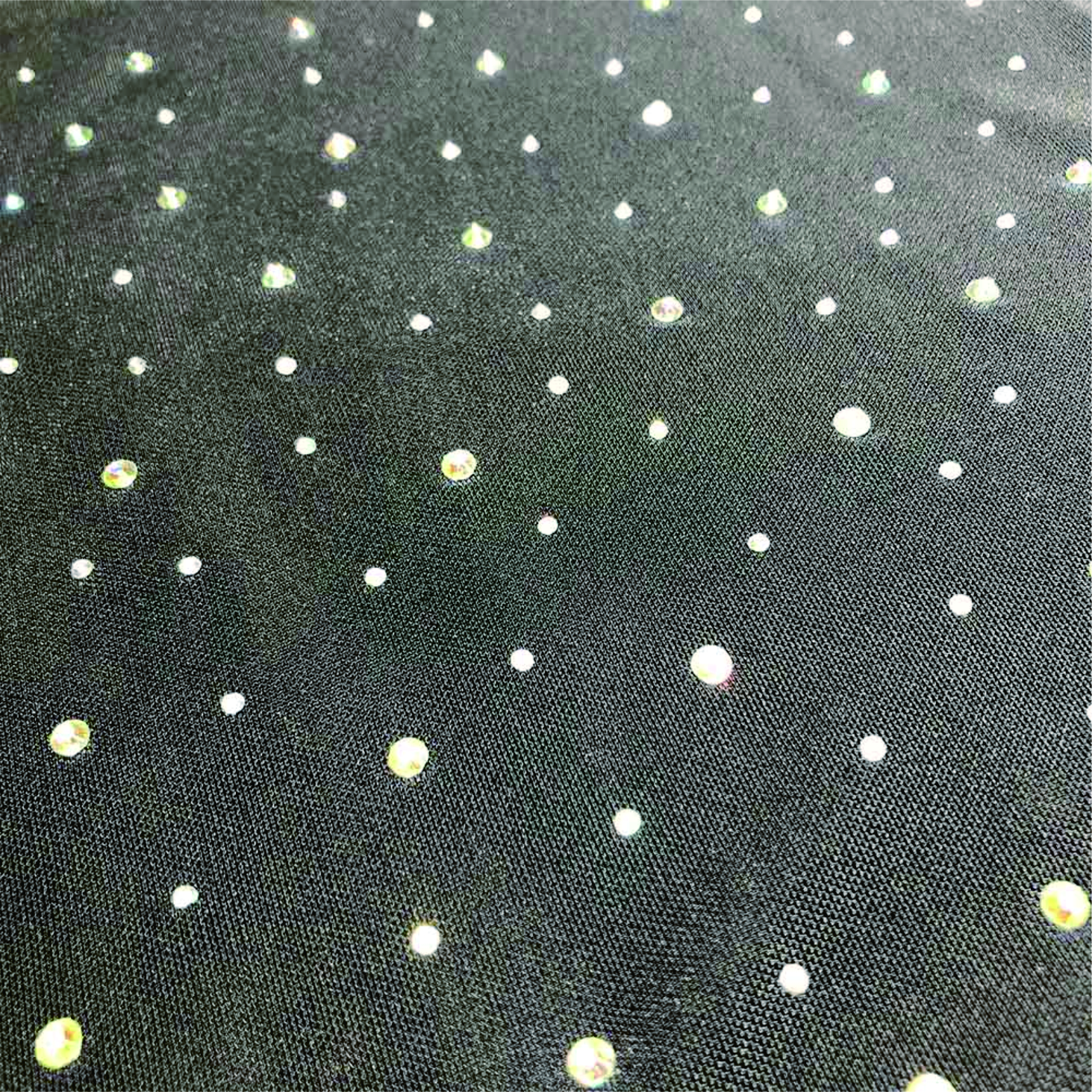
Heat-setting rhinestones
Heat-setting rhinestones is a widely used technique in pattern design. When subjected to high temperatures, the adhesive layer on the underside of the rhinestones melts and bonds to the fabric, resulting in a striking visual effect enhanced by colored or black and white rhinestones. There are various types of rhinestones available, including matte, glossy, colored, aluminum, octagonal, seed beads, caviar beads, and more. The size and shape of the rhinestones can be customized according to the design specifications.
Heat-setting rhinestones require elevated temperatures, making them unsuitable for lace fabrics, layered materials, and textured fabrics. If there is a significant size variation among the rhinestones, two separate placement patterns are necessary: first, the smaller rhinestones are set, followed by the larger ones. Additionally, silk fabrics may experience discoloration at high temperatures, and the adhesive on the underside of thin fabrics can easily seep through.
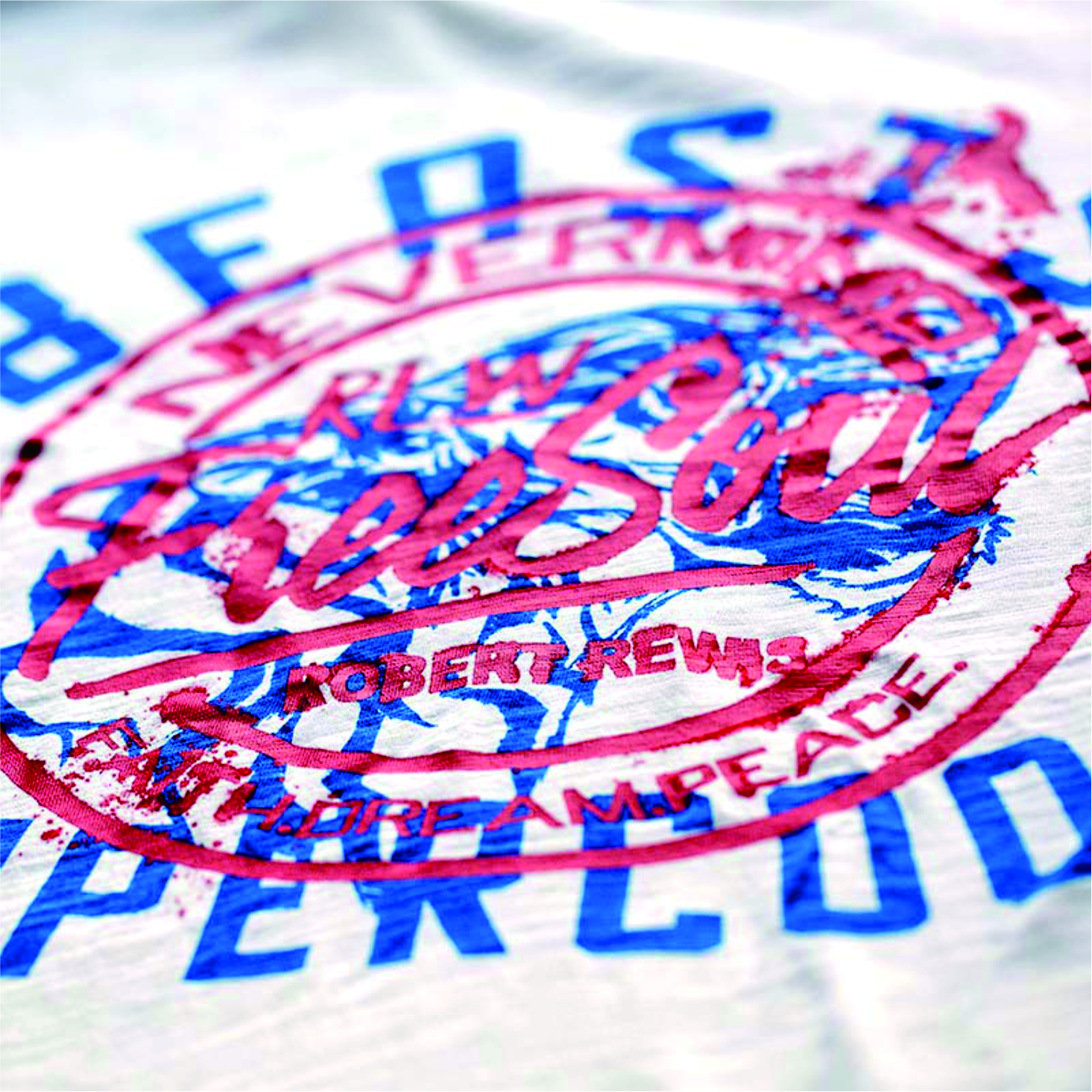
Rubber Print
This technique involves color separation and the use of a binder in the ink to ensure it adheres to the fabric surface. It is commonly employed and provides vibrant colors with excellent color fastness. The ink offers good coverage and is suitable for printing on a wide range of fabric types, regardless of their color intensity. After the curing process, it results in a soft texture, leading to a smooth and gentle feel. Furthermore, it demonstrates good elasticity and breathability, preventing the fabric from feeling constricted or causing excessive sweating, even when applied to large-scale printing.
Suitable for: Cotton, linen, viscose, rayon, nylon, polyester, polypropylene, spandex, and various blends of these fibers in clothing.
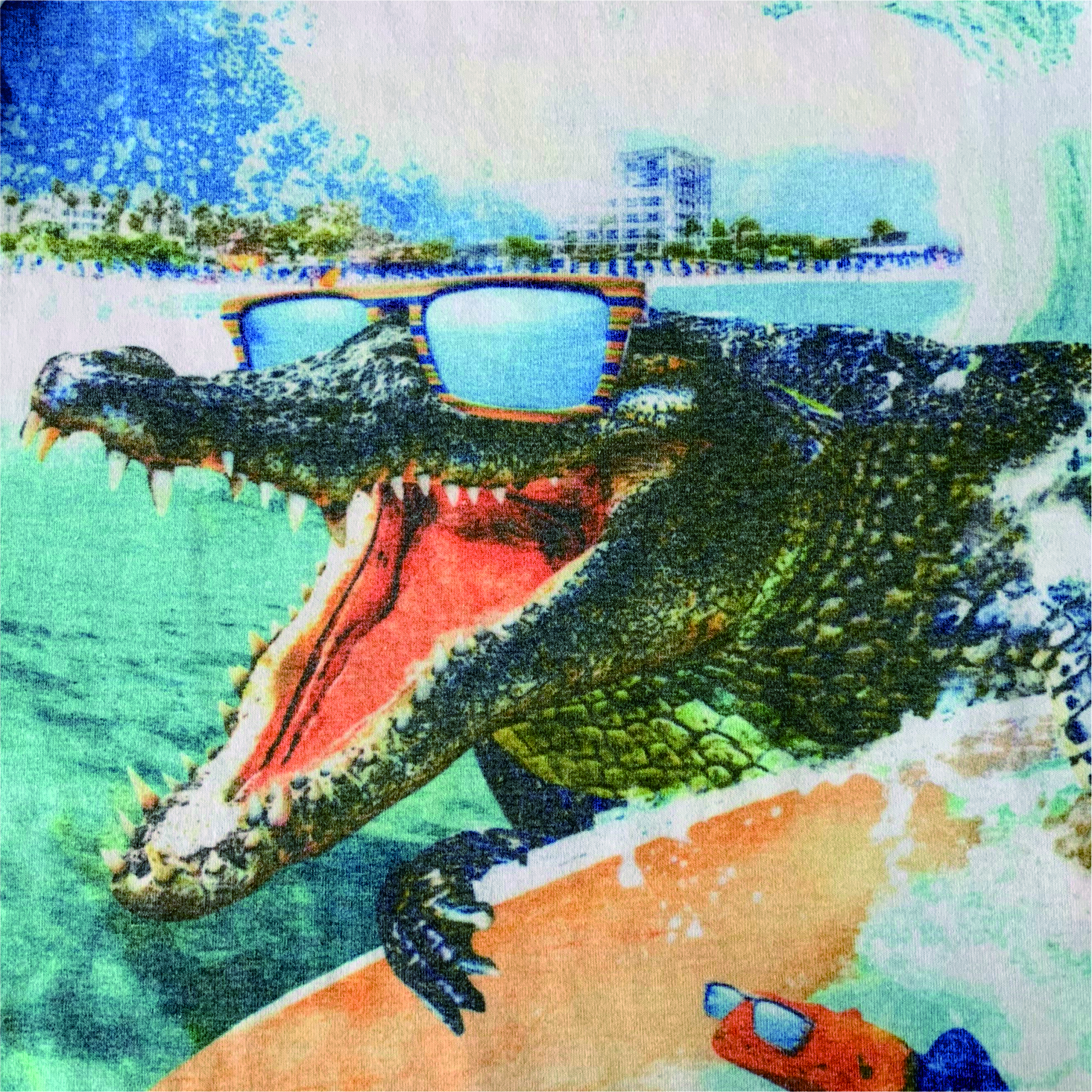
Sublimation print
It is a cutting-edge digital printing method that transforms solid dyes into a gaseous state, allowing them to be infused into fabric fibers for pattern printing and coloring. This technique enables colors to be embedded within the fiber structure of the fabric, resulting in vibrant, long-lasting designs with excellent breathability and softness.
During the sublimation printing process, a specialized digital printer and sublimation inks are utilized to print the desired design onto specially coated transfer paper. The transfer paper is then firmly pressed onto the fabric intended for printing, with appropriate temperature and pressure applied. As heat is introduced, the solid dyes convert into gas and penetrate the fabric fibers. Upon cooling, the dyes solidify and become permanently embedded within the fibers, ensuring that the pattern remains intact and does not fade or wear off.
In comparison to digital printing, sublimation printing is particularly suited for fabrics with a higher polyester fiber content. This is because sublimation dyes can only bond with polyester fibers and do not yield the same results on other fiber types. Additionally, sublimation printing is generally more cost-effective than digital printing.
Suitable for: Sublimation printing is commonly used for a variety of garments, including T-shirts, sweatshirts, activewear, and swimwear.
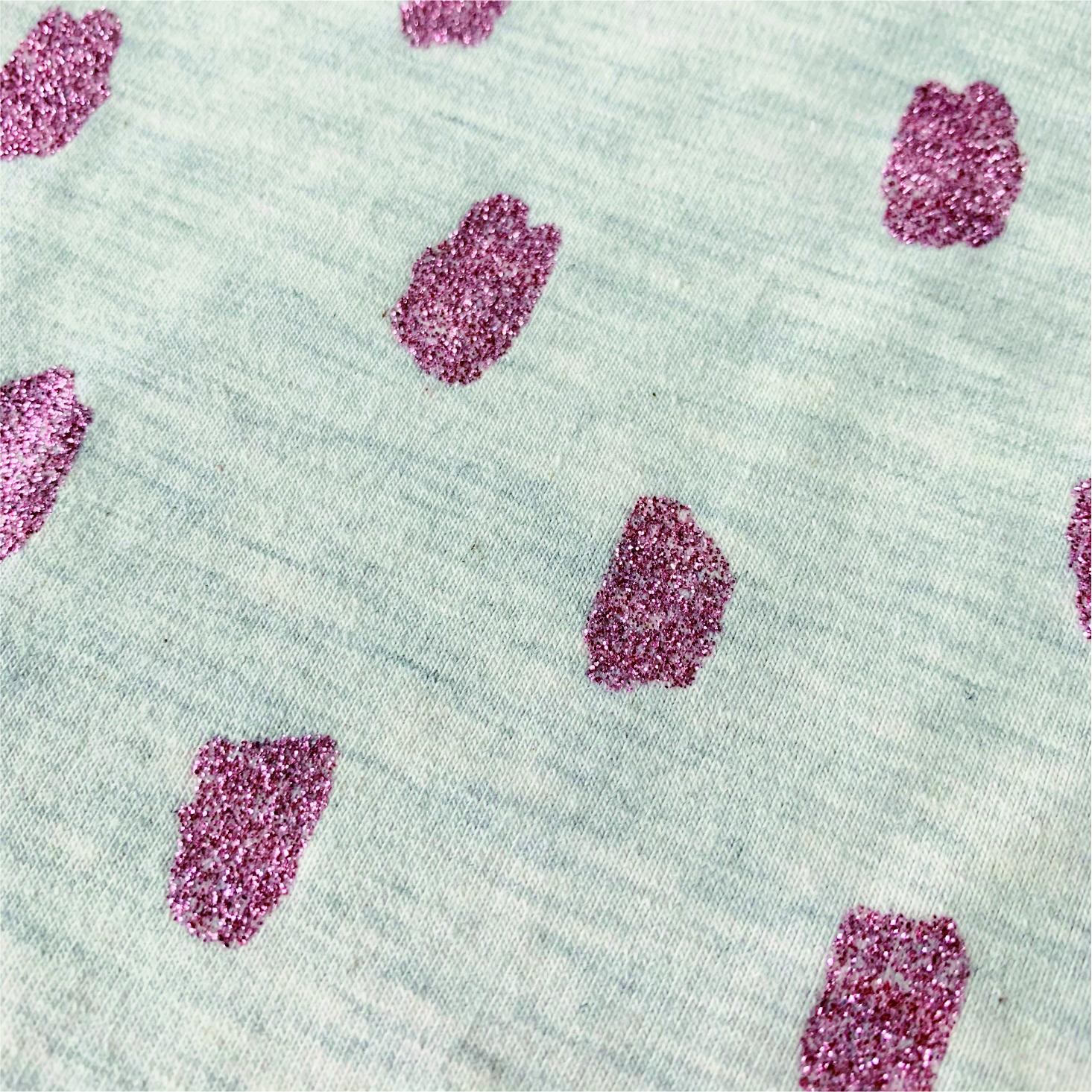
Glitter Print
Glitter Print is a printing method that produces a dazzling and vibrant effect on garments by applying glitter to the fabric. It is frequently utilized in fashion and eveningwear to introduce a distinctive and eye-catching shimmer, enhancing the visual allure of the clothing. In comparison to foil printing, glitter printing provides a more budget-friendly option.
During the glitter printing process, a specialized adhesive is first applied to the fabric, followed by an even sprinkling of glitter onto the adhesive layer. Pressure and heat are then employed to securely bond the glitter to the fabric surface. After the printing is finished, any excess glitter is gently shaken off, resulting in a consistent and sparkling design.
Glitter print generates an enchanting shimmer effect, infusing garments with energy and brilliance. It is commonly used in girls’ apparel and teenage fashion to add a hint of glamour and sparkle.
RECOMMEND PRODUCT